РБК+ / Территория бизнеса
Программа рассказывает о зоне комфортной для создания и развития бизнеса. Программах поддержки бизнеса, создании инфраструктуры развития, инвестициях.
Участником программы могут быть как компании, создающие и развивающие бизнес-инфраструктуру (например, компании, инвестирующие в строительство бизнес-центров), так и города, и регионы, развивающие и поддерживающие бизнес на своей территории, свободные экономические зоны, промышленные предприятия и зоны развивающие и поддерживающие малый и средний бизнес на подведомственных территориях, либо компании интегрирующие малые предприятия в свою производственную инфраструктуру.
Выпуск за 9 августа

Бережливое производство в автомобилестроении
Алина Танатарова, обозреватель:
— Принципы бережливого производства придумали японские автопроизводители в конце 1980-х. В России первым предприятием, адаптировавшим эту концепцию к условиям отечественного производства, стал Горьковский автомобильный завод. Произошло это в начале 2000-х. В этой программе мы расскажем о том, как производственная система ГАЗ стала философией постоянных улучшений, как она влияет на промышленную экономику и людей. И о том, как опыт одного завода повлиял на развитие различных отраслей в стране»
Наша съемочная группа приехала в Нижний Новгород, здесь работает завод ГАЗ. На площади в 600 гектар расположились цеха, в которых производят транспорт для грузовых и пассажирских перевозок, коммунального хозяйства, а также для социальных учреждений.
Алина Танатарова, обозреватель:
— Перед вами главная проходная. Именно из этих ворот выезжает самый востребованный коммерческий автомобиль страны «Газель», а когда-то выезжали легковые «Победа», «Волга», «Чайка». Предприятие, как и вся страна, за свою историю пережило немало потрясений: распад СССР, череду экономических кризисов. В 1990-х производство было на грани банкротства, но появились новый собственник и новые решения, в их числе бережливое производство. Современную историю завода узнаем у работников ГАЗа.
ГАЗ стал пионером бережливого производства в стране. В начале 2000-х собственник предприятия Олег Дерипаска побывал на заводах Toyota, там он увидел, как особая форма организации труда позволяет снижать издержки и улучшать качество продукции. В 2003 году на ГАЗе уже работали японские специалисты, они помогали российским коллегам постичь философию так называемых кайдзенов, «улучшений» в переводе с японского.
— В чем главный принцип, суть подхода бережливого производства?
Игорь Краснов, руководитель производства грузовых автомобилей ГАЗа:
— Человек всегда должен быть в эпицентре внедрения всех улучшений, и вот забота о человеке, исключение ненужных действий — это и есть суть, стандартизированная работа и использование других инструментов производственной системы.
— С чего начинали весь этот процесс по улучшению?
— Был определен эталонный участок, на тот момент я работал начальником участка, и в общем, принимал личное участие в результате одного из проектов.
Вот благодаря реализации кайдзен, который мы на тот момент внедрили, получилось повысить производительность труда практически вдвое, сократить запасы на рабочих местах в несколько раз.
— Получается, что 20 лет назад эта идея была новаторской на рынке автомобилестроения?
— Безусловно, запасы на этом конвейере составляли тогда два дня. Представляете, сейчас они составляют два часа и при этом исключены простои по внутренней логистике. Вот что позволяет производственная система.
Первые кайдзены внедрялись на участке сварки ветрового проема в цехе сборки и сварки цельнометаллического кузова «Газели». В этом лично принимал участие Олег Дерипаска: наблюдал за процессом с хронометром, анализировал производственные операции, искал потери и способы, как их избежать.
Олег Дерипаска, промышленник:
— По поводу занятости, производительности, вы же когда-то посещали ГАЗ. Помните старые поточные линии, там корпус. А сейчас от этого корпуса остается 10%, где стоят пятикоординатные станки, и один человек ими управляет, а двое обслуживают, перенастраивают. И работают непрерывно.
Производственная система работает уже 20 лет и доказала свою эффективность. Ежегодно внедряются более 7 тыс. улучшений во всех цехах, 20 участков становятся эталонными, а производительность труда растет не менее чем на 5%, создавая экономический эффект свыше полумиллиарда рублей.
Андрей Софонов, директор ГАЗа:
— У каждого оператора, который на этом конвейере работает, существует рабочий стандарт, по которому он должен выполнить операцию за время такта конвейера. Эта операция разбита на малые элементы от 3 до 10 секунд для того, чтобы можно было, анализируя работу этого оператора, увидеть потери, которые есть в цикле. Например, когда оператор вынужден подходить к стеллажу брать детали, после этого совершать переход для установки этой детали на автомобиль. То есть мы знаем, что это проблема, поэтому задача максимально, как вы видите, приблизить рабочее место оператора, то есть непосредственно к установке деталей на раму или автомобиль.
— А кто контролирует весь этот оркестр, кто дирижер?
— Это уже сформировавшаяся структура. Все сотрудники, включая директора предприятия, они все прошли обучение производственной системе.
Чтобы заводской «оркестр» играл в унисон, в бережливую систему должны быть включены все сотрудники, рассказывают в компании.
Оксана Исакова, директор по производственной системе группы ГАЗ:
— Пример ГАЗа показывает, что вовлечение сотрудников в процесс улучшений — это, прежде всего, личная ответственность руководителя, его заинтересованность в долгосрочном развитии себя, предприятия, страны. Это и есть одно из основных направлений развития производственной системы. Личная ответственность руководителей, личная вовлеченность, личный пример.
Елена работает на предприятии 22 года. Сегодня она бригадир конвейера подсборки кабин, тогда, в 2000-х, работала бригадиром по «тянущей» системе, поэтому ее первые кайдзены касались деталей: для каждой изобрели спецтару, этот кайдзен применяется и по сей день. Девушка вспоминает, как коллектив отреагировал на нововведения.
Елена Фомина, бригадир конвейера подсборки кабин ГАЗа:
— С энтузиазмом вначале никто не отнесся, но постепенно люди привыкли. Начали свое что-то предлагать, наблюдать в работе кому как удобнее. Кайдзенов было очень много. Это больше сотни, работа, конечно, командная в основном. Так как мы начинали с нуля, это и улучшение условий труда, это переходы, это 5S. Ну, дальше кайдзены стали масштабны, более интересные.
В основе любого кайдзена лежит принцип: сначала потерю найди, затем ее устрани. Например, в цехе окраски выявили риск ошибки оператора, которая могла привести к деформации крыши кузова. Раньше если подъемное устройство не было возвращено в исходное положение, то следующий кузов упирался в захват подъемника. Поэтому установили специальный датчик, который исключил такие ошибки. Подобные улучшения — инициатива самих работников. Все они проходят обучение производственной системе в Академии ГАЗа.
Галина Бирюкова, директор Академии современных технологий автомобилестроения им. А.Н. Моисеева:
— Мы выбрали уникальный метод практикоориентированный, когда обучение — это так называемое обучение боем, обучение на практике. В обучении производственной системе у нас минимум теории, всего около 10%, в основном это практика. Причем практика там, где есть проблемы, будь то производственный цех, производственный участок, бригада или офис. И соответственно, на данный момент мы делимся своим опытом, обучаем не только сотрудников ГАЗа, но и наших партнеров по бизнесу.
Соответствие нашим стандартам и принципам ПС у поставщиков, наших подрядчиков — это главное условие нашей работы с ними.
Одним из таких подрядчиков стал завод по производству автомобильных сидений. Потребность в оптимизации возникла в 2021 году, когда возрос спрос на продукцию.
Алексей Николенко, главный инженер ООО «НИАС»:
— Мы обратились за помощью к специалистам ГАЗа, для того чтобы нам помочь расшить так называемые узкие места. Первая группа, которая работала на участке сварки, рассмотрела вариант стандартизированной работы, и, сняв хронометражные наблюдения, было подмечено, что оптимально организовать работу на трех рабочих местах. Это дало увеличение буквально через 3,5 недели на 67% выпуска изделий. По участку сборки специалисты ГАЗа организовали нам конвейер ручной сборки сидений — то, чего у нас раньше не было, раньше работали восемь человек, потом стали работать уже шесть человек.
В Академии ГАЗа обучают не только специалистов из автоиндустрии. Предприятие расширяет применение производственной системы и за пределы отрасли.
Олег Дерипаска, промышленник:
— Страну создаст бизнес, страну создаст именно вовлечение в экономические отношения за счет результатов экономического роста как можно большей части населения Российской Федерации.
Бережливый подход уже успешно применяется в строительстве, логистике, в финансовом секторе, и даже в медицинских учреждениях. Поликлиника в Нижнем Новгороде внедряет кайдзены с 2017 года. Эта система особенно помогла во время пандемии.
Валентина Цывова, главный врач Центра медицинской профилактики ГАЗа:
— Во время ковида было очень много звонков от пациентов: из 100 звонков мы могли принять только 56%. Это, конечно, было очень неудобно нашим пациентам и нам, всех это раздражало. Вот поэтому мы сотрудников call-центра от окна переместили в определенные помещения, сделали многоканальные телефоны. На каждый из телефонов поставили цветовые лампочки для того, чтобы было понятно, что идет звонок, и чтобы не отвлекались медрегистраторы от приема пациентов. То есть мы разделили потоки, стало очень удобно, мы стали принимать практически 100%. Работают в call-центре пять человек, и они справляются. Мы совершенно четко разграничили, какие вопросы нужно задать пациенту. Это для того, чтобы впоследствии врач знал, кому совсем плохо и к кому ехать в первую очередь. Сократилось время приема звонков примерно в восемь раз.
Бережливое производство за 20 лет своего существования в стране из японского ноу-хау превратилось уже в российскую парадигму мышления. Опыт ГАЗа применяется в самых разных отраслях, он позволил осознать, что никакие передовые методы и технологии не будут работать без поддержки инженеров, бригадиров, операторов, слесарей, токарей, фрезеровщиков и многих других. Именно сотрудники и их желание менять и улучшать делают компанию конкурентоспособной и ведут к развитию экономики.
Бережливое производство в автомобилестроении
Алина Танатарова, обозреватель:
— Принципы бережливого производства придумали японские автопроизводители в конце 1980-х. В России первым предприятием, адаптировавшим эту концепцию к условиям отечественного производства, стал Горьковский автомобильный завод. Произошло это в начале 2000-х. В этой программе мы расскажем о том, как производственная система ГАЗ стала философией постоянных улучшений, как она влияет на промышленную экономику и людей. И о том, как опыт одного завода повлиял на развитие различных отраслей в стране»
Наша съемочная группа приехала в Нижний Новгород, здесь работает завод ГАЗ. На площади в 600 гектар расположились цеха, в которых производят транспорт для грузовых и пассажирских перевозок, коммунального хозяйства, а также для социальных учреждений.
Алина Танатарова, обозреватель:
— Перед вами главная проходная. Именно из этих ворот выезжает самый востребованный коммерческий автомобиль страны «Газель», а когда-то выезжали легковые «Победа», «Волга», «Чайка». Предприятие, как и вся страна, за свою историю пережило немало потрясений: распад СССР, череду экономических кризисов. В 1990-х производство было на грани банкротства, но появились новый собственник и новые решения, в их числе бережливое производство. Современную историю завода узнаем у работников ГАЗа.
ГАЗ стал пионером бережливого производства в стране. В начале 2000-х собственник предприятия Олег Дерипаска побывал на заводах Toyota, там он увидел, как особая форма организации труда позволяет снижать издержки и улучшать качество продукции. В 2003 году на ГАЗе уже работали японские специалисты, они помогали российским коллегам постичь философию так называемых кайдзенов, «улучшений» в переводе с японского.
— В чем главный принцип, суть подхода бережливого производства?
Игорь Краснов, руководитель производства грузовых автомобилей ГАЗа:
— Человек всегда должен быть в эпицентре внедрения всех улучшений, и вот забота о человеке, исключение ненужных действий — это и есть суть, стандартизированная работа и использование других инструментов производственной системы.
— С чего начинали весь этот процесс по улучшению?
— Был определен эталонный участок, на тот момент я работал начальником участка, и в общем, принимал личное участие в результате одного из проектов.
Вот благодаря реализации кайдзен, который мы на тот момент внедрили, получилось повысить производительность труда практически вдвое, сократить запасы на рабочих местах в несколько раз.
— Получается, что 20 лет назад эта идея была новаторской на рынке автомобилестроения?
— Безусловно, запасы на этом конвейере составляли тогда два дня. Представляете, сейчас они составляют два часа и при этом исключены простои по внутренней логистике. Вот что позволяет производственная система.
Первые кайдзены внедрялись на участке сварки ветрового проема в цехе сборки и сварки цельнометаллического кузова «Газели». В этом лично принимал участие Олег Дерипаска: наблюдал за процессом с хронометром, анализировал производственные операции, искал потери и способы, как их избежать.
Олег Дерипаска, промышленник:
— По поводу занятости, производительности, вы же когда-то посещали ГАЗ. Помните старые поточные линии, там корпус. А сейчас от этого корпуса остается 10%, где стоят пятикоординатные станки, и один человек ими управляет, а двое обслуживают, перенастраивают. И работают непрерывно.
Производственная система работает уже 20 лет и доказала свою эффективность. Ежегодно внедряются более 7 тыс. улучшений во всех цехах, 20 участков становятся эталонными, а производительность труда растет не менее чем на 5%, создавая экономический эффект свыше полумиллиарда рублей.
Андрей Софонов, директор ГАЗа:
— У каждого оператора, который на этом конвейере работает, существует рабочий стандарт, по которому он должен выполнить операцию за время такта конвейера. Эта операция разбита на малые элементы от 3 до 10 секунд для того, чтобы можно было, анализируя работу этого оператора, увидеть потери, которые есть в цикле. Например, когда оператор вынужден подходить к стеллажу брать детали, после этого совершать переход для установки этой детали на автомобиль. То есть мы знаем, что это проблема, поэтому задача максимально, как вы видите, приблизить рабочее место оператора, то есть непосредственно к установке деталей на раму или автомобиль.
— А кто контролирует весь этот оркестр, кто дирижер?
— Это уже сформировавшаяся структура. Все сотрудники, включая директора предприятия, они все прошли обучение производственной системе.
Чтобы заводской «оркестр» играл в унисон, в бережливую систему должны быть включены все сотрудники, рассказывают в компании.
Оксана Исакова, директор по производственной системе группы ГАЗ:
— Пример ГАЗа показывает, что вовлечение сотрудников в процесс улучшений — это, прежде всего, личная ответственность руководителя, его заинтересованность в долгосрочном развитии себя, предприятия, страны. Это и есть одно из основных направлений развития производственной системы. Личная ответственность руководителей, личная вовлеченность, личный пример.
Елена работает на предприятии 22 года. Сегодня она бригадир конвейера подсборки кабин, тогда, в 2000-х, работала бригадиром по «тянущей» системе, поэтому ее первые кайдзены касались деталей: для каждой изобрели спецтару, этот кайдзен применяется и по сей день. Девушка вспоминает, как коллектив отреагировал на нововведения.
Елена Фомина, бригадир конвейера подсборки кабин ГАЗа:
— С энтузиазмом вначале никто не отнесся, но постепенно люди привыкли. Начали свое что-то предлагать, наблюдать в работе кому как удобнее. Кайдзенов было очень много. Это больше сотни, работа, конечно, командная в основном. Так как мы начинали с нуля, это и улучшение условий труда, это переходы, это 5S. Ну, дальше кайдзены стали масштабны, более интересные.
В основе любого кайдзена лежит принцип: сначала потерю найди, затем ее устрани. Например, в цехе окраски выявили риск ошибки оператора, которая могла привести к деформации крыши кузова. Раньше если подъемное устройство не было возвращено в исходное положение, то следующий кузов упирался в захват подъемника. Поэтому установили специальный датчик, который исключил такие ошибки. Подобные улучшения — инициатива самих работников. Все они проходят обучение производственной системе в Академии ГАЗа.
Галина Бирюкова, директор Академии современных технологий автомобилестроения им. А.Н. Моисеева:
— Мы выбрали уникальный метод практикоориентированный, когда обучение — это так называемое обучение боем, обучение на практике. В обучении производственной системе у нас минимум теории, всего около 10%, в основном это практика. Причем практика там, где есть проблемы, будь то производственный цех, производственный участок, бригада или офис. И соответственно, на данный момент мы делимся своим опытом, обучаем не только сотрудников ГАЗа, но и наших партнеров по бизнесу.
Соответствие нашим стандартам и принципам ПС у поставщиков, наших подрядчиков — это главное условие нашей работы с ними.
Одним из таких подрядчиков стал завод по производству автомобильных сидений. Потребность в оптимизации возникла в 2021 году, когда возрос спрос на продукцию.
Алексей Николенко, главный инженер ООО «НИАС»:
— Мы обратились за помощью к специалистам ГАЗа, для того чтобы нам помочь расшить так называемые узкие места. Первая группа, которая работала на участке сварки, рассмотрела вариант стандартизированной работы, и, сняв хронометражные наблюдения, было подмечено, что оптимально организовать работу на трех рабочих местах. Это дало увеличение буквально через 3,5 недели на 67% выпуска изделий. По участку сборки специалисты ГАЗа организовали нам конвейер ручной сборки сидений — то, чего у нас раньше не было, раньше работали восемь человек, потом стали работать уже шесть человек.
В Академии ГАЗа обучают не только специалистов из автоиндустрии. Предприятие расширяет применение производственной системы и за пределы отрасли.
Олег Дерипаска, промышленник:
— Страну создаст бизнес, страну создаст именно вовлечение в экономические отношения за счет результатов экономического роста как можно большей части населения Российской Федерации.
Бережливый подход уже успешно применяется в строительстве, логистике, в финансовом секторе, и даже в медицинских учреждениях. Поликлиника в Нижнем Новгороде внедряет кайдзены с 2017 года. Эта система особенно помогла во время пандемии.
Валентина Цывова, главный врач Центра медицинской профилактики ГАЗа:
— Во время ковида было очень много звонков от пациентов: из 100 звонков мы могли принять только 56%. Это, конечно, было очень неудобно нашим пациентам и нам, всех это раздражало. Вот поэтому мы сотрудников call-центра от окна переместили в определенные помещения, сделали многоканальные телефоны. На каждый из телефонов поставили цветовые лампочки для того, чтобы было понятно, что идет звонок, и чтобы не отвлекались медрегистраторы от приема пациентов. То есть мы разделили потоки, стало очень удобно, мы стали принимать практически 100%. Работают в call-центре пять человек, и они справляются. Мы совершенно четко разграничили, какие вопросы нужно задать пациенту. Это для того, чтобы впоследствии врач знал, кому совсем плохо и к кому ехать в первую очередь. Сократилось время приема звонков примерно в восемь раз.
Бережливое производство за 20 лет своего существования в стране из японского ноу-хау превратилось уже в российскую парадигму мышления. Опыт ГАЗа применяется в самых разных отраслях, он позволил осознать, что никакие передовые методы и технологии не будут работать без поддержки инженеров, бригадиров, операторов, слесарей, токарей, фрезеровщиков и многих других. Именно сотрудники и их желание менять и улучшать делают компанию конкурентоспособной и ведут к развитию экономики.
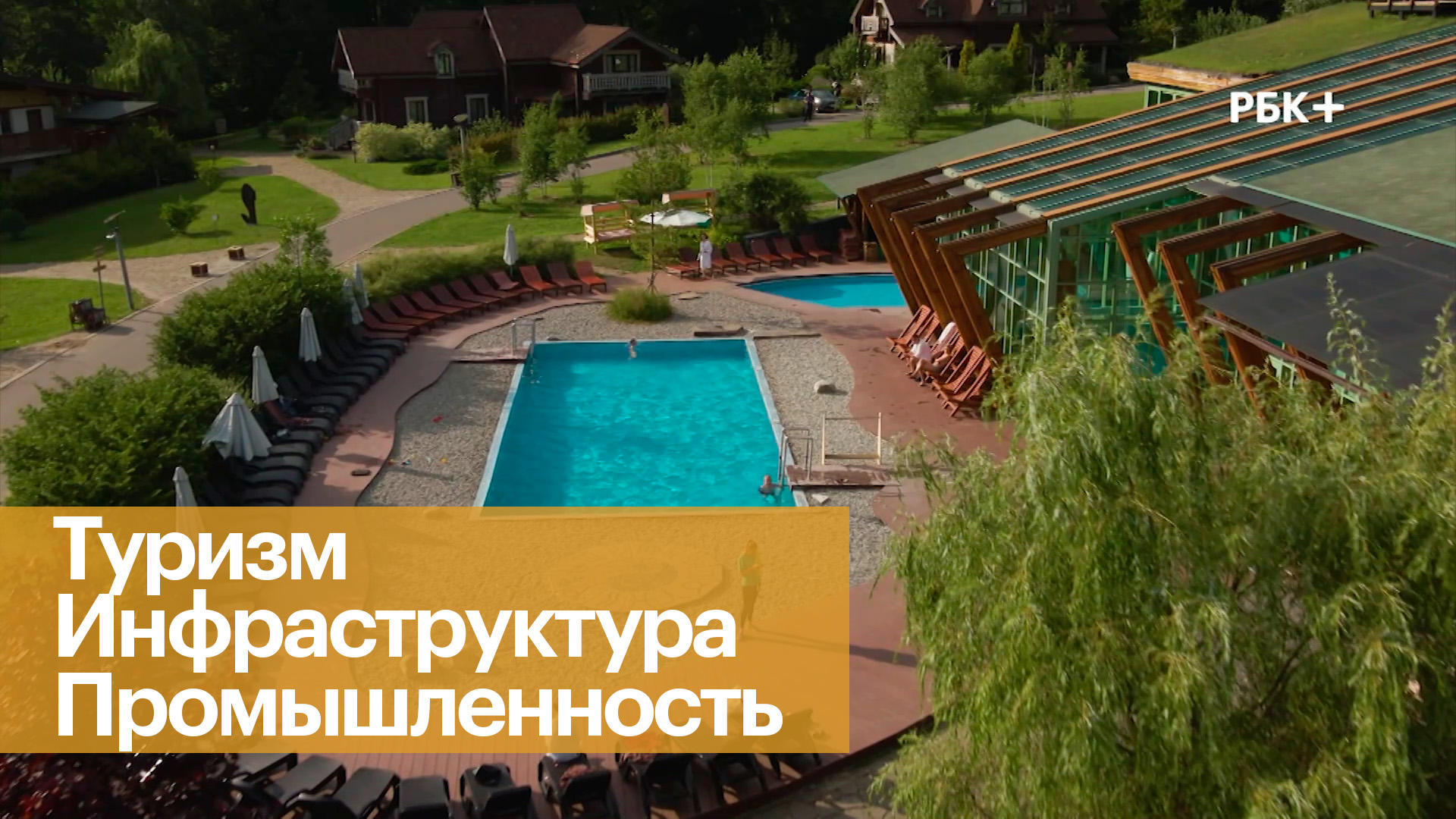
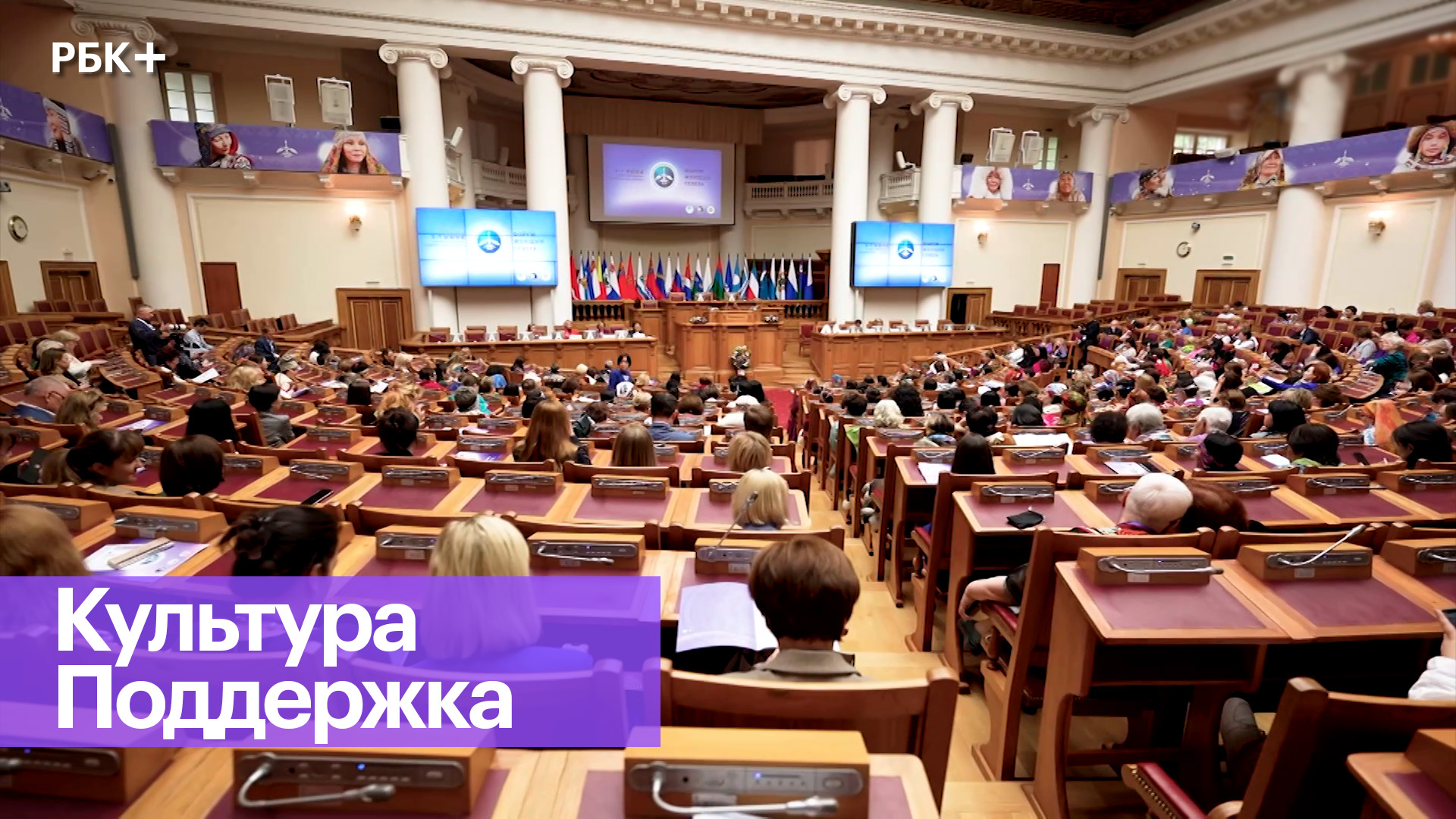

